Printed Circuit Board Assembly (PCBA)
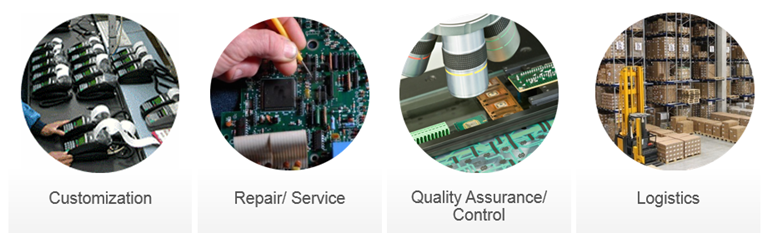
Magnum provides complete value added services including warehousing, customization of POS terminal/pin-pad devices and repair & service of field-returned devices with highest quality standards in fully secured environment.
Customization of POS System
Magnum maintains 6 production lines to APCA standards and approved by the banks to customize POS terminal. Magnum has the capacity to handle 10,000 devices per month (Upgradable to 20,000/month). The customization process usually includes:
- Loading bank security keys through KMIS procedure with the help of secure IT infrastructure
- Loading and setting up bank specific application
- Modifying pin-pad facial, adding lenses and labels with bank logos
- Adding serial number labels and other tracking labels as per bank requirements
- Adding accessories – load cables, power supplies, connectors, stands etc
- Individual packing of terminal and accessories as per the spec
Magnum customize POS devices for most of the banks including CBA, ANZ, Westpac, St. George, and other merchants.
Repair & Service Facility
- State of the art soldering, de-soldering and fault diagnostic equipment
- Antistatic environment
- Trained and qualified technicians
- Managed by experienced managers and supervisors
- Documentation of repair procedure/manual and work instructions
- Effective quality assurance system
- In-house developed software system to track the history of all repaired devices and generates report on different faults & SLAs
- Log-in/log-out into the system
- Running test software and fault diagnosis
- Carry out the required repairs – electrical and mechanical
- Replacement of parts
- Full refurbishment of POS machines
- Component level repair of the electronic boards
- Maintain inventory of spare parts
- Follow the service level agreement such as
- 10 days turnaround
- Zero dead on arrival
- Zero packing issues
- Customer communication on agreed levels and many more
Bounded Warehousing & Distribution Hub
Magnum offers warehousing and logistics services to its customers including operations of distribution hub from bounded/duty-free facilities. Magnum maintains warehousing in Sydney and Johor Bahru. The services offered includes:
- Handling goods by Ocean, Air and Road transportation
- Follow up with freight forwarders and organize custom clearance
- Receive, unload, carry out the counting and other incoming quality check and report to the OEM
- Stacking pallets and entering shipment details into the system
- Receiving and executing dispatch orders on behalf of OEM
- Communication with OEM with all issues of incoming and outgoing deliveries
- Carry out periodic stock verification and reporting to OEM
- Attending to OEM officials/auditors for stock verification activities
- Maintain tracking databases for all stock movements
Testing
- In-circuit testing
- Functional testing
- Special testing as specified by the customers
- Reliability testing such as burn-in and temperate cycle
- Improvement testing such as yield reporting and defect prevention
Quality Management
We follow continuous improvement procedures throughout the manufacturing process to perfect our quality. All working procedures and instructions are well documented and audited periodically. Staff training and development is always on the priority list so that the quality of our people reflects in the quality of the product that we deliver to our customers.
QUALITY CONTROL SYSTEM
- Documentation and document control system
- Engineering Change Order (ECO) and implementation
- Customer complaint analysis
- Corrective actions and implementation
- Statistical process control for continuous improvement
- Non conformance listing, reporting and control
QUALITY STANDARDS
We follow the standards as below in different areas:
- ANSI/ISO/ASQ 9001:2008 and ISO 13485:2003
- ISO10012-1 and ANSI-Z540-1 – Calibration
- IPC-A-610E Class 2,3
- ANSI/ESD S20.20-1999 – ESD Control
Manufacturing Facilities
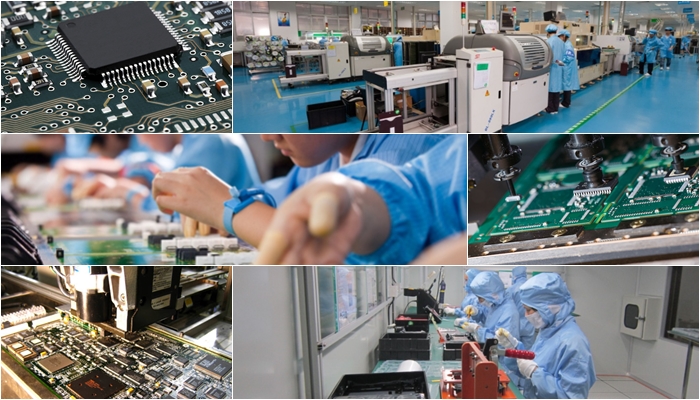
Certification
